7 Steps to Benchmark Areas and Improve Safety Performance
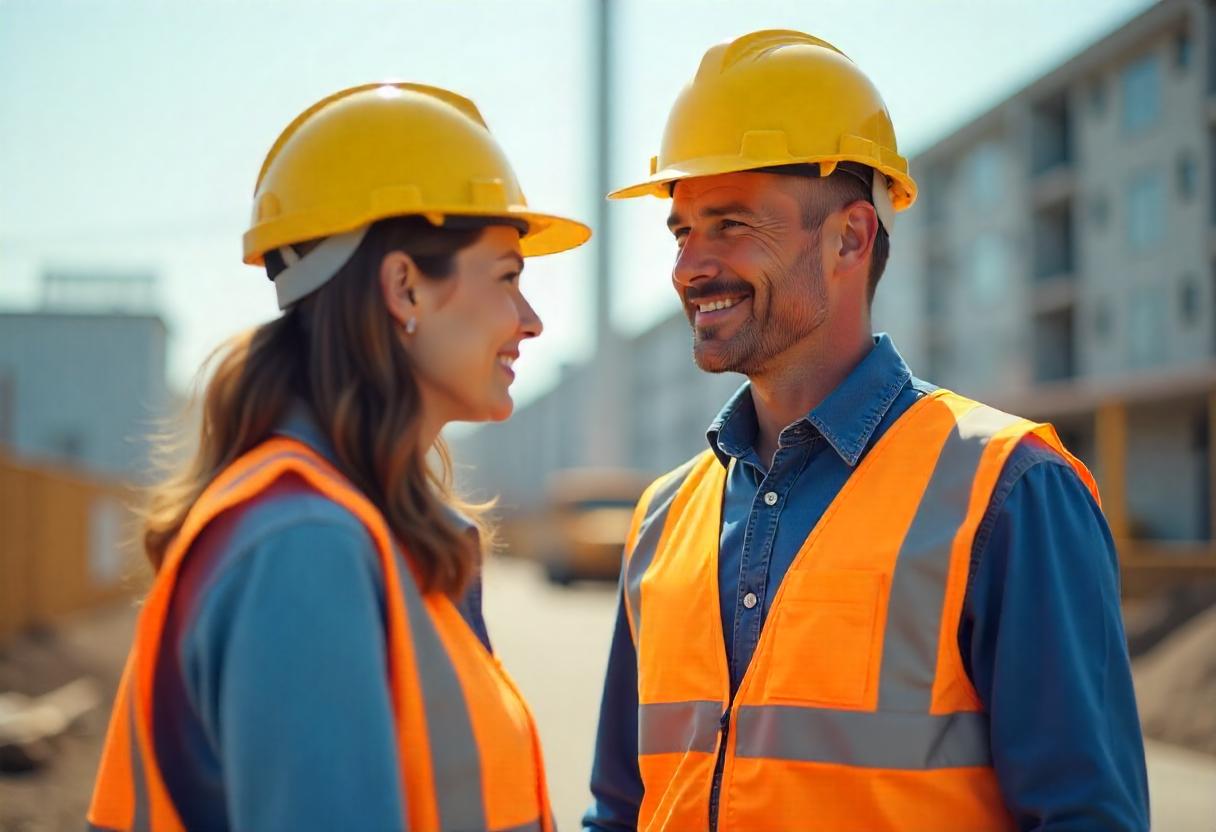
When we talk about workplace hazards, many people think of accidents that “just happen.” The truth is, most incidents can be prevented if we look closely at how we manage our safety performance. A factory supervisor once shared how they thought their workshop was “safe enough” until a small incident exposed unseen risks. That moment pushed them to start benchmarking their safety measures. By comparing their practices with recognized standards and continuously improving, they saw fewer injuries and happier employees.
Before we dive into the steps, it’s worth noting that many professionals in industrial cities are now looking for ways to upskill through a Safety Course in Multan. These programs are designed to help workers and managers understand hazards better, interpret benchmarking results, and turn them into real improvements. For anyone working in manufacturing plants or construction sites, learning locally has proven to be a great way to adopt global best practices.
Why Benchmarking Matters in Workplace Safety
Benchmarking is not just about comparing numbers; it’s about learning from the best. Imagine walking into a workshop where tools are scattered, wires are loose, and warning signs are missing. Then picture another place where everything is labeled, hazards are flagged, and workers follow clear safety routines. Which one feels more secure? Benchmarking helps you turn your workplace into that second example by setting clear standards and aiming to meet or exceed them.
In hazardous environments, such as chemical plants or heavy equipment zones, even a small lapse can lead to serious injuries. Therefore, understanding these steps will empower you to create safer spaces for everyone.
Step 1: Identify Key Areas That Need Benchmarking
The first step is to look around your workplace and list areas with potential risks. Are there machines that require regular maintenance? Are workers handling chemicals without proper ventilation? Start by collecting incident reports and safety inspection records.
For instance, in one logistics company, management noticed a recurring problem with workers lifting heavy boxes incorrectly. By marking this as a priority area for benchmarking, they were able to introduce new lifting techniques and equipment, drastically reducing back injuries.
Step 2: Set Clear and Measurable Safety Standards
Once you know which areas to focus on, the next step is to define what “good” looks like. Setting measurable goals makes improvement easier. Instead of saying “reduce accidents,” say “reduce hand injuries by 20% within six months.”
A construction site manager once shared how they turned vague instructions into specific rules, like mandating high‑visibility vests and weekly tool checks. Over time, their site became known for having one of the lowest accident rates in the region.
Step 3: Gather Data and Observe Current Practices
Now, spend time observing how tasks are actually carried out. Take notes, talk to employees, and review inspection checklists. This step often reveals gaps you might not see on paper.
In a food processing plant, an internal audit showed that while written protocols were excellent, some workers skipped steps due to time pressure. This discovery gave the team a starting point for targeted training and process redesign.
Step 4: Compare with Industry Leaders
Benchmarking means learning from others who are doing it better. Look at recognized safety standards in your field. Attend local seminars, read case studies, or visit facilities with excellent records.
For example, an automotive plant once invited a safety consultant who had worked with global leaders in manufacturing. By applying those insights, they introduced new machine‑guarding methods and reduced downtime caused by accidents.
Step 5: Engage Your Workforce in the Process
Safety is not something you can enforce top‑down; it must be embraced by everyone. Organize workshops, encourage feedback, and involve staff in finding solutions.
One anecdote from a textile factory stands out: management held monthly “safety chats” where workers shared near‑miss experiences. These discussions not only built trust but also uncovered small hazards before they became major issues.
Step 6: Implement Changes and Monitor Progress
After gathering insights and setting goals, start implementing improvements. This may include updating equipment, changing workflows, or providing additional training. Keep track of how these changes impact incident rates and worker feedback.
In one engineering workshop, after implementing a new system for chemical storage, they saw a 40% drop in minor spills within three months. Tracking such progress keeps everyone motivated to maintain high standards.
Step 7: Review, Learn, and Refine
Safety benchmarking is not a one‑time task. Schedule regular reviews to measure progress against your goals. What worked well? What still needs attention? By making these reviews part of your routine, you ensure that your workplace evolves alongside new challenges and technologies.
A packaging company in an industrial zone discovered that regular quarterly reviews helped them catch equipment wear‑and‑tear early, preventing accidents before they occurred. This ongoing loop of learning created a culture where safety became second nature.
Turning Insights into Action
When you follow these seven steps, you’re not just meeting regulations—you’re actively creating a safer environment for your team. This proactive approach also boosts productivity, as fewer accidents mean less downtime and fewer compensation claims.
In cities where industry is rapidly growing, such as Multan, many organizations are investing in professional training to keep up. A Safety Course in Multan offers not just theoretical knowledge but also practical sessions that show how benchmarking and hazard identification work in real life. These programs often become the foundation for long‑term safety improvements.
Read more about how a safety officer diploma can enhance your skills and open new opportunities in industrial safety management.
Final Thoughts
Improving safety performance through benchmarking is not complicated, but it does require commitment. By identifying key areas, setting clear standards, gathering and comparing data, involving your team, implementing changes, and reviewing regularly, you build a strong foundation for a safer workplace.
Remember, every step you take toward better safety is a step toward protecting lives, reducing hazards, and building a culture of care. Start today, and watch your workplace transform into an environment where people feel secure, valued, and motivated to perform at their best.