Cost of Fuel Storage Tanks: A Comprehensive Guide
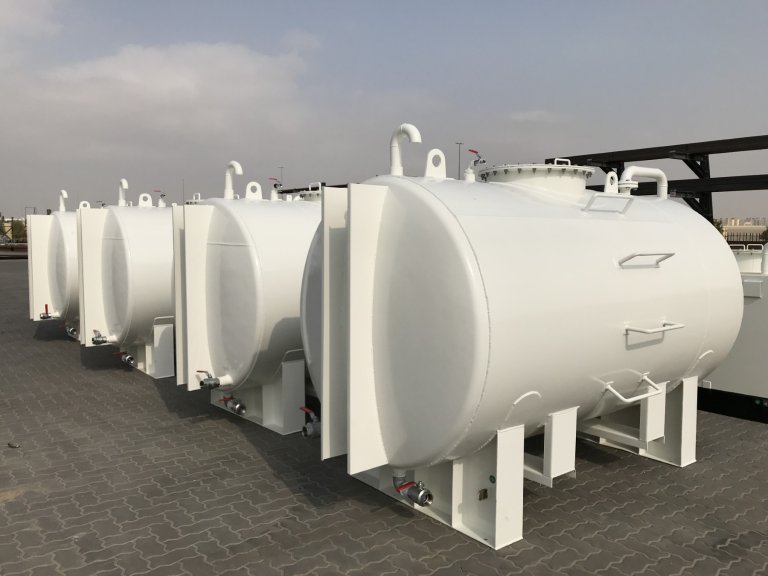
Fuel storage tanks are critical for industries, commercial facilities, fuel distributors, and emergency operations worldwide. Understanding the cost of fuel storage tanks is essential for planning, budgeting, and compliance with safety standards.
What Are Fuel Storage Tanks?
Fuel storage tanks are engineered containers used to store petroleum products, diesel, petrol, kerosene, aviation fuel, and other flammable liquids. They are available in aboveground and underground designs, with varying capacities, configurations, and material types to meet operational needs.
Factors Affecting the Cost of Fuel Storage Tanks
1. Tank Material
The material is the most significant determinant of price. The most common materials are:
- Carbon Steel Tanks: Durable, suitable for large-capacity storage, and cost-effective. Priced between USD 1.50 and USD 2.50 per litre.
- Stainless Steel Tanks: Corrosion-resistant, ideal for aviation fuel and sensitive petroleum products. Cost ranges from USD 2.80 – 4.50 per litre.
- Fibreglass Reinforced Plastic (FRP) Tanks: Lightweight, corrosion-resistant, used for underground storage to prevent leaks. The average price is USD 3.00 – 4.20 per litre.
- Polyethene Tanks: Used mainly for small portable fuel storage. Cost is USD 1.20 – 1.80 per litre.
2. Tank Capacity
The capacity impacts cost linearly and economically due to the scale of fabrication:
- Small tanks (500 – 5,000 litres): Approx USD 1,000 – 7,500.
- Medium tanks (5,000 – 30,000 litres): Approx USD 7,500 – 50,000.
- Large industrial tanks (30,000 – 200,000 litres): Approx USD 50,000 – 300,000, depending on configuration, site access, and installation requirements.
3. Tank Type
- Aboveground Tanks (ASTs): Less expensive due to lower installation complexity. Typical cost ranges between USD 1.20 and 2.50 per litre.
- Underground Tanks (USTs): Higher cost due to excavation, environmental compliance, leak detection, and corrosion protection systems. Approx USD 2.50 – 4.50 per litre.
4. Design Specifications
Custom-designed tanks for pressurised storage, double-walled containment, fire protection, anti-corrosion coatings, internal linings, or seismic compliance significantly increase cost.
- Single-Wall Tanks: Basic storage with minimal installation requirements.
- Double-Wall Tanks: Includes a secondary containment layer. Adds 20-40% extra cost compared to single-wall designs.
- Horizontal Cylindrical Tanks: Standard design for ASTs.
- Vertical Cylindrical Tanks: Used for large capacities to reduce footprint, generally USD 10,000 – 30,000 higher than equivalent horizontal designs due to engineering complexity.
5. Installation Costs
- Aboveground Installation: Includes site preparation, foundation pads, and safety barriers. Cost ranges from USD 3,000 – 20,000 based on site conditions.
- Underground Installation: Involves excavation, backfill, concrete encasement, piping, leak detection, and environmental assessments. Costs USD 20,000 – 150,000 depending on capacity and depth.
6. Compliance and Certification
Tanks must meet API 650, UL 142, UL 2085, NFPA 30, or regional standards. Certification adds 5-15% to fabrication cost but ensures safety and regulatory compliance.
Detailed Fuel Tank Cost Examples
Tank Type Material Capacity (Litres)Approx Cost (USD)
Aboveground Horizontal Carbon Steel 5,000 6,500 – 9,000
Aboveground Horizontal Stainless Steel 5,000 12,000 – 18,000
Underground Double-Wall FRP 10,000 30,000 – 42,000
Underground Double-Wall Steel with FRP Coating 20,000 55,000 – 80,000
Vertical Cylindrical Carbon Steel 100,000 150,000 – 210,000
Maintenance Costs to Consider
Beyond procurement, maintenance is critical for long-term operational integrity:
- Inspection and Testing: Annual inspections, thickness testing, and compliance certifications cost USD 500 – 5,000 per tank, depending on size and local regulations.
- Repairs and Coatings: Recoating, corrosion repairs, or structural welding cost USD 2,000 – 15,000 based on extent.
- Leak Detection Systems: For USTs, periodic testing and system replacement every 10 years costs USD 5,000 – 20,000.
Key Suppliers and Fabricators
Leading global fuel tank suppliers include:
- CST Industries (USA) – Large vertical bolted tanks.
- Tank Connection (USA) – Field-welded and factory-welded tanks.
- Permian Tank (USA) – ASME-coded steel tanks.
- Westeel (Canada) – Aboveground fuel storage solutions.
- Fuelchief (New Zealand) – Bunded diesel tanks with global supply.
How to Reduce Fuel Storage Tank Costs
- Accurate Sizing: Avoid oversizing tanks beyond operational need to reduce material and installation costs.
- Standard Designs: Opt for off-the-shelf designs instead of full customisation.
- Bulk Orders: Multiple tank orders reduce per-unit fabrication and logistics costs.
- Supplier Location: Choosing a local supplier reduces freight and import duties.
- Pre-Engineered Foundations: For ASTs, using pre-cast foundation pads reduces civil works costs.
Environmental and Safety Compliance Costs
Environmental agencies worldwide impose strict safety, leak prevention, and spill containment standards. Non-compliance can result in heavy fines, operational shutdowns, and environmental restoration costs. Always include:
- Spill Containment Berms
- Emergency Venting
- Overfill Protection Systems
- Fire Safety Equipment
Typically, these add 10-20% additional cost but are essential for operational approval and insurance coverage.
Future Trends in Fuel Storage Tanks
- Smart Monitoring Systems: Real-time fuel level and leak detection monitoring is becoming standard.
- Hybrid Designs: Combining renewable energy storage with fuel storage systems.
- Enhanced Coatings: Longer-lasting internal linings to reduce maintenance frequency.
- Modular Tank Farms: Faster deployment using pre-fabricated modular tank designs.
Conclusion
The cost of fuel storage tanks varies significantly based on material, capacity, design, installation type, and compliance requirements. A clear understanding of specifications and operational needs enables businesses to plan effective fuel storage systems within budget while ensuring safety, compliance, and operational efficiency.