How to Ensure Clean Burning of Industrial Fuel Oil
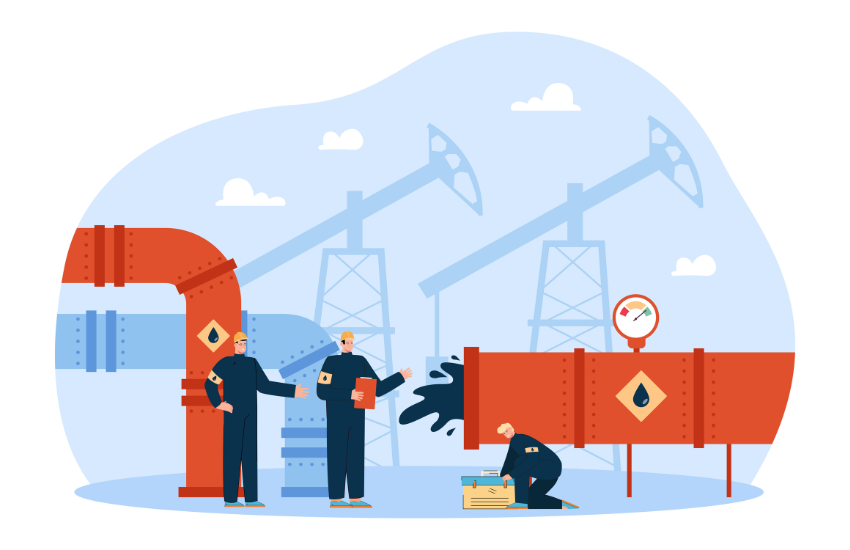
Clean burning of industrial fuel oil is more than just a matter of operational efficiency—it’s crucial for reducing harmful emissions, extending equipment life, and complying with stringent UK environmental regulations. Whether you’re managing an industrial boiler, generator, or a heating system, ensuring that your fuel burns cleanly is essential to minimising costs, avoiding fines, and maintaining sustainability.
This article is crafted to provide practical, human-centred insights—blending industry best practices with real-world applications to guide UK industries towards cleaner combustion.
Why Clean Burning Matters in the UK Industrial Sector
In the United Kingdom, the pressure on industries to reduce their carbon footprint and particulate emissions has never been higher. Clean burning of industrial fuel oil plays a vital role in:
- Complying with DEFRA and UK-EU environmental regulations
- Maximising thermal efficiency
- Reducing maintenance costs and unplanned downtime
- Preventing soot build-up and boiler scaling
- Lowering NOx, SOx, and particulate matter emissions
Whether your facility is located in an urban area like Birmingham or a rural site in Yorkshire, maintaining optimal combustion is key for both compliance and operational success.
1. Choose High-Quality Industrial Fuel Oil
The first and perhaps most important step to ensure clean burning is selecting the right grade and quality of industrial fuel oil. Not all fuels are created equal.
🔍 Look for:
- Low sulphur content: UK law mandates the use of low sulphur fuels to reduce sulphur dioxide emissions.
- Certified suppliers: Always source from trusted UK industrial fuel oil suppliers with EN-standard products.
- Consistent batch quality: Irregular quality can cause burner misfiring, carbon deposits, and efficiency drops.
💡 Pro Tip: Ask your supplier for a certificate of analysis (CoA) for each delivery to monitor viscosity, sulphur content, and other vital parameters.
2. Use the Right Burners and Nozzles
Burner configuration can make or break your combustion performance.
- Ensure burner compatibility with the type of industrial fuel oil you’re using.
- Use low-NOx burners where possible to reduce nitrogen oxide emissions.
- Regularly calibrate nozzles for optimal spray patterns to avoid uneven burning and carbon residues.
Burners designed for heavy fuel oils or multi-fuel options can offer flexibility while maintaining clean combustion under variable load conditions.
3. Maintain Proper Air-to-Fuel Ratios
Clean burning requires a carefully controlled mix of air and fuel. Too much air (lean combustion) results in energy loss; too little air (rich combustion) leads to soot, carbon monoxide, and unburned fuel.
How to optimise:
- Use oxygen trim systems to automatically adjust airflow based on real-time combustion conditions.
- Install flue gas analysers to monitor O₂, CO₂, and CO levels.
- Regularly tune the burners based on seasonal variations, especially during the UK’s colder months.
🛠 Tip: Monthly adjustments during winter and bi-annual adjustments in milder months keep combustion sharp year-round.
4. Invest in Fuel Pre-Heating and Conditioning
Some industrial fuel oils—especially heavier grades—require pre-heating for proper atomisation.
- Pre-heating reduces fuel viscosity, improving spray consistency and air-fuel mixing.
- Pre-warming lines and burners in colder UK climates prevents blockages and start-up smoke.
- Consider using fuel additives approved by UK environmental agencies to aid combustion and reduce emissions.
These additives break down carbon chains, promote cleaner burning, and reduce fouling in combustion chambers.
5. Regular Equipment Maintenance Is Non-Negotiable
Dirty filters, clogged nozzles, and fouled heat exchangers all contribute to incomplete combustion.
Routine tasks include:
- Cleaning burner tips and air inlets
- Inspecting and replacing fuel filters
- Removing soot build-up in combustion chambers
- Checking for signs of corrosion or leaks in fuel lines
A quarterly maintenance schedule is ideal for medium-to-high-use systems. For 24/7 operations, consider monthly inspections.
6. Monitor Emissions with Smart Technology
The UK government encourages the use of Continuous Emissions Monitoring Systems (CEMS) to ensure that emissions stay within limits and that fuel is being burned cleanly.
- Real-time feedback helps facilities react before violations occur.
- Long-term data logs can be useful for audits and performance tracking.
- Integration with building management systems enhances automation.
Modern smart meters can alert operators to inefficiencies or combustion irregularities before they cause major problems.
7. Train Your Operators
Even with the best equipment, poorly trained personnel can compromise clean burning efforts.
- Provide certified combustion and fuel handling training.
- Include troubleshooting workshops for burner adjustment and maintenance.
- Keep staff updated on evolving UK environmental regulations and technologies.
This human factor is often the most overlooked element in combustion efficiency.
Final Thoughts: Clean Burning as a Competitive Edge
In a competitive UK industrial landscape, ensuring the clean burning of industrial fuel oil goes beyond compliance—it reflects operational excellence, environmental responsibility, and financial prudence.
When you combine high-quality fuel, well-maintained equipment, intelligent monitoring, and skilled personnel, your organisation not only reduces emissions but also gains a sustainable edge. Whether you run a manufacturing plant in Manchester or a logistics hub in London, clean combustion is the cleaner, smarter path forward.