Key Reliability Checks to Ensure Flawless PCB Design in OrCAD X
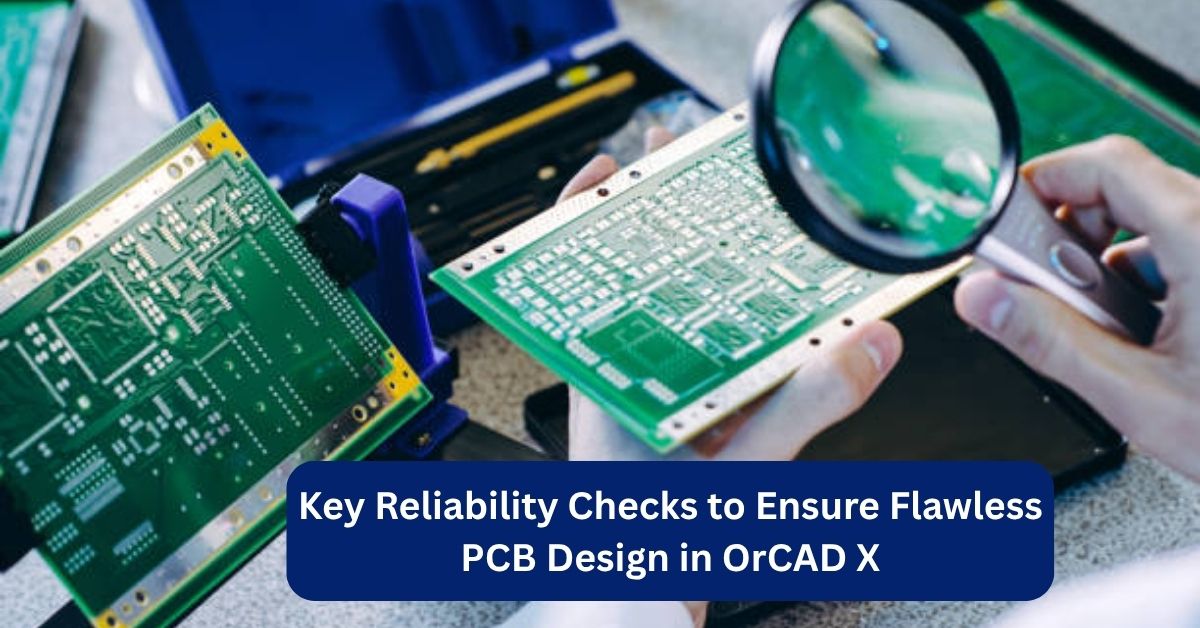
In today’s high-stakes world of electronic design, delivering a product that meets performance expectations is only half the battle. Ensuring it does so reliably—under real-world conditions and long-term use—is what separates a quality PCB from a failed one. For any OrCAD PCB designer, understanding the critical reliability checks within the design process is no longer optional; it’s a must for creating fail-proof, future-ready designs.
As electronics continue to shrink and demands on performance skyrocket, design teams are relying on advanced toolsets and methodologies to validate every detail before the first prototype is built. This article explores the key reliability checks that form the backbone of any robust PCB design, with a focus on how modern platforms like OrCAD X facilitate this evolving process.
Why Reliability Checks Are Non-Negotiable in Modern PCB Design
In the competitive electronics market, failure isn’t just expensive—it’s reputation-damaging. Reliability checks ensure that every trace, via, and component in a design will function as intended, regardless of environmental stress, thermal load, or manufacturing variability.
Some key reasons reliability checks are integral to every project include:
- Preventing field failures and recalls
- Meeting industry compliance standards (IPC, MIL-STD, etc.)
- Ensuring design integrity across temperature and humidity ranges
- Reducing time and cost associated with redesigns
Whether you’re building a high-speed data board or a simple embedded controller, reliability begins at the design level—and is enforced through specific validation strategies.
Top Reliability Checks Every OrCAD PCB Designer Should Implement
1. Electrical Rule Checking (ERC)
Before digging into signal quality or power integrity, it’s essential to ensure the basic electrical rules of the design are sound. ERC examines key parameters such as:
- Unconnected nets or pins
- Short circuits
- Overlapping power domains
- Incomplete reference connections
An OrCAD PCB designer can avoid countless hours of rework by resolving ERC issues during schematic review before layout even begins.
2. Design Rule Checking (DRC)
Once the schematic is clean, the layout must follow specific design rules tailored to the manufacturing process. DRC validation typically includes:
- Trace spacing and width
- Via and pad clearance
- Component placement restrictions
- Layer stackup consistency
Ignoring DRC guidelines not only causes fabrication delays but can lead to latent defects that only appear after deployment.
3. Signal Integrity (SI) Analysis
High-speed digital designs, especially those involving DDR memory, USB, or PCIe interfaces, must pass signal integrity checks. SI analysis identifies:
- Reflections and overshoot
- Crosstalk between adjacent traces
- Delay mismatches in differential pairs
- Ringing or noise margins violations
Many designers rely on simulation tools that integrate with layout environments to evaluate SI behavior in real time.
4. Power Integrity (PI) Analysis
As circuits become more compact, the need for clean and stable power delivery becomes increasingly critical. Power integrity checks ensure:
- Low impedance across the power delivery network (PDN)
- Proper decoupling capacitor placement
- Voltage droop under dynamic loads
- Minimal ground bounce
Addressing these challenges early ensures that the design won’t suffer from voltage drops that could disrupt sensitive components.
5. Thermal Reliability Assessment
Thermal management is one of the most underappreciated aspects of reliability. Designs may function well at room temperature but fail under load or in hot environments. Key thermal checks include:
- Heat map visualization of component hotspots
- PCB stackup optimization for heat dissipation
- Use of thermal vias and copper pours
- Verification against thermal derating curves
Thermal simulation tools integrated within modern design platforms allow designers to make informed decisions about component placement and heatsink requirements.
6. Creepage and Clearance Validation
Especially important in high-voltage or mixed-signal designs, ensuring proper creepage and clearance distances helps avoid dielectric breakdown and arcing. Checks should account for:
- Surface vs. air clearance
- Material properties and pollution degree
- Industry safety standards (UL, IEC)
These checks are crucial in industrial or automotive applications where high voltage isolation is required.
7. Manufacturability and Assembly Checks
A reliable design must also be buildable. Design for Manufacturability (DFM) and Design for Assembly (DFA) checks ensure that:
- Pads are aligned correctly with component footprints
- There’s enough solder mask between pads
- Components are oriented to match automated placement requirements
- Silk screens don’t overlap with solder pads
At this stage, engineers also consider Design for Test (DFT), ensuring that test points and diagnostics are integrated into the layout.
Automation’s Role in Performing Reliability Checks
Modern design tools streamline the reliability verification process using built-in automation and rule-based engines. These features allow a designer to define thresholds and constraints that reflect manufacturing and performance requirements. For instance:
- Automatic rule checks upon saving or running layout simulations
- Real-time flagging of DRC or SI violations
- Reports that highlight potential risks by severity
These automated features help OrCAD PCB designers catch issues early, saving both time and development costs.
Using OrCAD X for Streamlined Reliability Verification
The design ecosystem has evolved rapidly, with modern platforms offering far more than schematic capture and routing. Tools like OrCAD X integrate simulation, reliability validation, and reporting within a single environment—providing a seamless experience for hardware engineers.
In fact, for those seeking deeper insights into the specific capabilities and reliability-driven workflows of OrCAD X, this blog post offers a complete breakdown of its tools and how they contribute to seamless, error-free PCB design.
By aligning your workflow with such toolsets, you can significantly cut down debugging time and focus on optimizing design performance rather than firefighting failures.
Common Pitfalls That Compromise PCB Reliability
Despite best efforts, designers sometimes overlook key issues that compromise long-term reliability:
- Neglecting component derating: Operating components too close to their maximum ratings shortens lifespan.
- Improper trace impedance: Failing to match impedance on differential pairs results in signal degradation.
- Ignoring thermal reliefs: Overheated zones can cause solder joint failures.
- Poor documentation: Lack of clear design intent or test plans leads to errors during handoff.
Preventing these pitfalls requires a combination of experience, automation, and awareness of evolving best practices.
Best Practices for Future-Proof Reliability
To meet modern reliability standards and build scalable designs, consider implementing the following:
- Establish Design Rules Early: Collaborate with manufacturers to set rules before layout begins.
- Use Real-Time Validation: Enable live rule checking in your layout tools.
- Integrate Testing Features: Include test points and diagnostics in every board iteration.
- Document Everything: From assumptions to tolerances, document your rationale and constraints clearly.
- Perform Peer Reviews: Regular schematic and layout reviews catch what tools may miss.
These steps don’t just enhance product quality—they speed up project timelines by reducing rework.
Conclusion: Reliability Is a Design Mindset
Flawless PCB design isn’t a product of chance—it’s the result of thoughtful planning, proven workflows, and continuous validation. For any OrCAD PCB designer, embedding reliability checks across the design process isn’t just a task, it’s a mindset. As the demands on electronics increase, adopting comprehensive design validation practices ensures that your products not only work—but last.
Whether you’re validating a multi-layer board for industrial use or fine-tuning a compact consumer device, the right tools and checks will elevate your design from good to great. Leveraging integrated reliability features in platforms like OrCAD X helps bridge the gap between design intent and real-world success.